周青等:汽车碰撞安全与轻量化研发中的若干挑战性课题
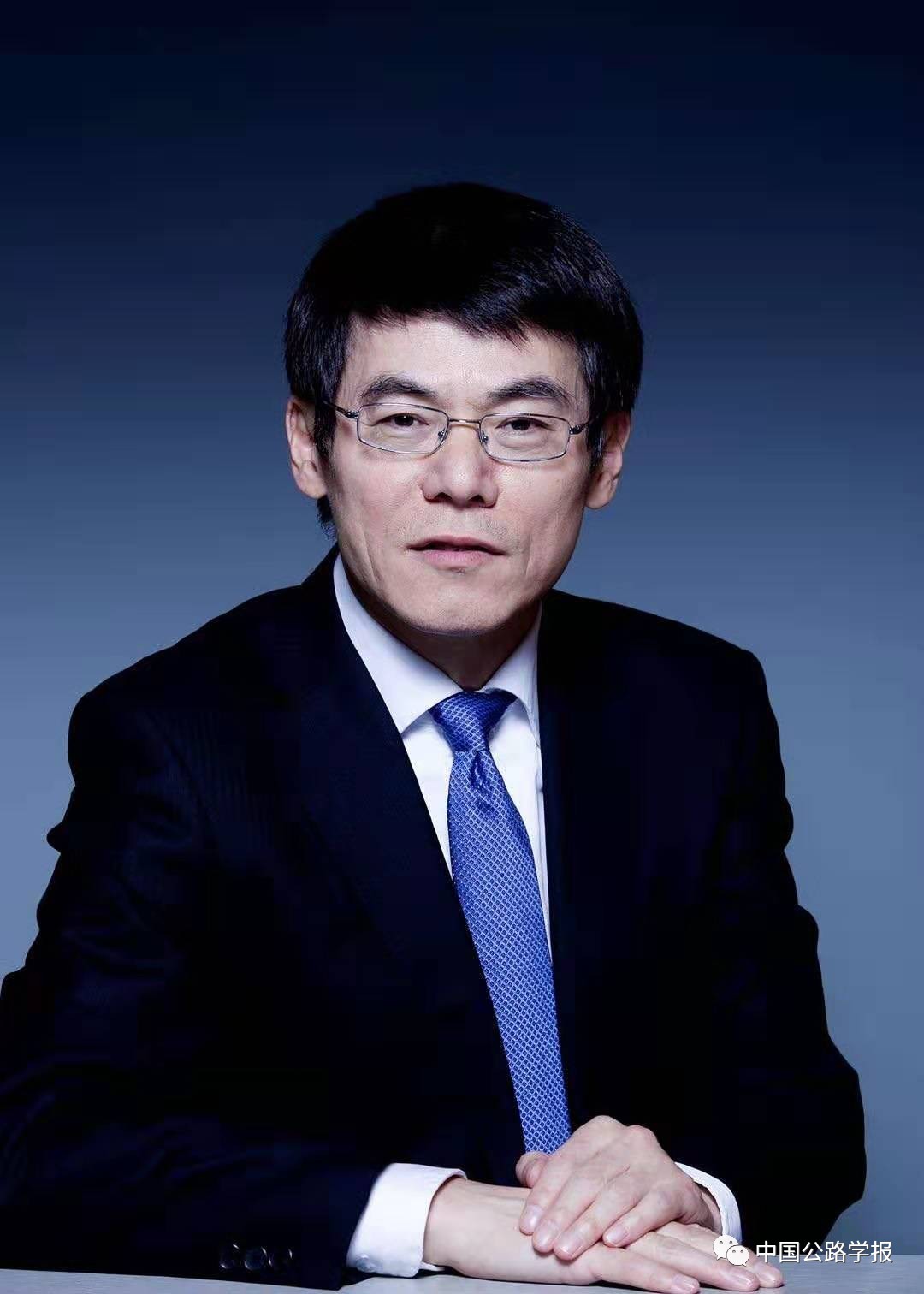
内容提要:
汽车结构与动力电池的碰撞安全性是开发轻量化、电动化汽车的强制性要求和关键的基础性支撑技术。本文通过三个方面的10个典型课题及结果,介绍并综述汽车碰撞安全性研发的技术挑战。
第一,采用夹层式汽车前舱罩盖技术,提升罩盖结构力学特性的横向均匀性以及冲击响应历程的均匀性,满足汽车吸能位移限定下的行人头部碰撞响应控制;采用精细人体有限元模型解析复杂工况下行人下肢损伤机理和影响参数,基于人体组织损伤层面的虚拟评估改进汽车结构的人体碰撞保护设计;面向复杂道路交通事故工况和多样化人体特征,解决强非线性条件下的自适应智能乘员保护系统优化设计难题,通过在时间和空间上对乘员约束载荷的均衡化实现针对工况可调的碰撞保护。
第二,揭示材料冲击测试中系统共振导致信号振荡和材料屈服放大振荡的机理,开发抑制信号振荡的轻质动态力传感器;精细表征材料在碰撞载荷和复杂应力状态下的力学行为,针对高强钢、塑料、胶粘和焊点等轻质高强材料及复合连接接头建立大变形失效断裂预报方法及仿真模型。
第三,基于动力电池多工况挤压试验,建立电池在外载荷作用下的材料失效、电压陡降与温度上升的响应特征关联性,提出一个用力学响应特征预测电池内部损伤起始和短路发生的判据,解决电池在机械滥用载荷下的短路预测问题,建立能准确预测电池变形响应的数值模型及碰撞安全评估方法,应用于电池包和电动车的轻量化与碰撞安全性设计。
0 引言
以轻量化和电动化为主导的汽车工业产业升级是提升中国制造能力的重要内容。汽车的小型化、轻量化、电动化和智能化给汽车碰撞安全性设计提出了更大的技术挑战。在汽车轻量化和电动化技术升级与应用中,与汽车碰撞事故中人员安全、结构安全以及动力电池安全相关的主要技术瓶颈体现在:
(1) 轻量化和小型化要求导致汽车碰撞刚度提高,缺乏道路事故工况和严苛碰撞波形下对行人及乘员提供有效保护的技术以及安全评测工具和设计方法,无法有效解决低成本车辆和小型车辆在碰撞吸能位移不足与降低乘员和行人伤亡风险之间的设计冲突;
(2) 缺乏对轻质高强材料和连接接头在碰撞载荷下的大变形断裂失效的力学性能表征和仿真技术,缺乏基于异种材料和复合连接的结构设计方法和断裂控制技术,无法保障复杂工况下轻量化车身和动力电池碰撞保护设计的质量和效率;
(3) 车用动力电池在碰撞冲击下变形破坏和内短路失效机理不明确,难以准确预测碰撞工况下动力电池的损伤和热失控风险,使得电池针对碰撞载荷经常处于“过保护”或“保护不足”的状态,不利于实现车辆轻量化。
新一代的汽车碰撞安全技术与传统技术有很大区别。传统开发方式以整车碰撞测试和逆向工程经验为主,新一代技术核心是把设计开发的重心和时间投入前移到材料和子结构层面,通过精细化的材料力学性能试验表征,在材料和结构层面上进行机理解析,其关键是通过碰撞仿真来预测材料和结构的失效,进而给出断裂抑制设计和轻量化设计,以此来提高整车碰撞仿真的精度,加快开发周期,降低成本。
基于本研究团队在过去十多年中的研究成果,本文通过10个研究课题及结果,论述汽车碰撞安全性研发中的若干技术挑战。这些研究课题的主体是汽车结构与动力电池系统的碰撞安全性设计,代表新一代汽车碰撞安全技术。这些难题来源于工程实际,基础是冲击力学理论,研究手段是材料和结构的冲击力学试验以及计算仿真分析。无论对象是人体结构,还是电池材料或电芯结构,亦或是高强钢B柱及焊点,我们都是研究其在碰撞载荷下的失效机理和损伤控制方法,建立高精度计算仿真模型,对其在冲击载荷下的变形与失效行为进行准确预测,并应用从时间和空间上均衡化其碰撞响应历程的思想,提升汽车碰撞安全保护性能,形成人体碰撞损伤分析与保护、轻量化结构碰撞失效控制与设计、以及车用动力电池碰撞失效预测及保护的技术体系。
本文所介绍的成果多是由本研究团队的国际合作课题和国家纵向课题产生,并结合国内汽车企业的研发需求,通过校企合作对相关方法和技术进行吸收转化,进一步研制出了具有自主知识产权的产业化应用技术,并应用于多款自主品牌的量产车型中,实现了国际开放合作创新基础上的自主应用。
1 复杂工况及吸能空间限定下的人体碰撞保护技术
1.1 满足行人头部碰撞保护要求的夹层式汽车前舱罩盖技术
在行人与汽车的碰撞事故中,汽车前舱罩盖须起到降低行人头部碰撞损伤风险的功能。罩盖下方空间狭小,碰撞吸能位移受限,以及传统的汽车前舱罩盖结构变形强度分布不均匀、碰撞吸能效率低下,是两个行人头部碰撞设计的主要技术挑战。
针对上述问题,我们发明的面向行人头部碰撞安全保护的均匀构型夹层汽车前舱罩盖结构技术[1-6](图 1、图 2)是一种有效且低成本的行人头部碰撞保护方式。其基本思想是,沿行人头部冲击方向,通过分析初始碰撞的惯性力和罩盖随动质量的影响设计控制初始碰撞波峰,之后碰撞抗力迅速下降;随着冲击位移的增大,罩盖膜力效应开始起作用,碰撞抗力再次上升;当罩盖下方的吸能空间用尽以后,以罩盖夹层的局部压溃来控制碰撞力的尾峰,吸收残余动能[2]。在罩盖的面内方向,根据行人头部碰撞响应过程主导因素不同,划分碰撞波形阶段与前舱罩盖特征区域,通过夹层结构形式和厚度分布补偿因边界约束等造成的罩盖变形刚度分布不均,实现罩盖碰撞响应全局最优。通过这样的结构设计思想,使得行人头碰撞保护所需的罩盖下方空间减少了20%。夹层式罩盖设计实现了头部模块碰撞历程的均匀化和罩盖横向刚度分布的均匀化,由此形成了行人头模块碰撞波形控制理论以及相应的夹层罩盖设计方法,能够同时突破罩盖变形强度不均和下方吸能位移受限两个难点。
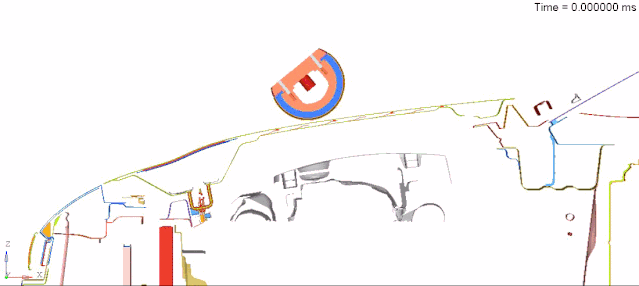
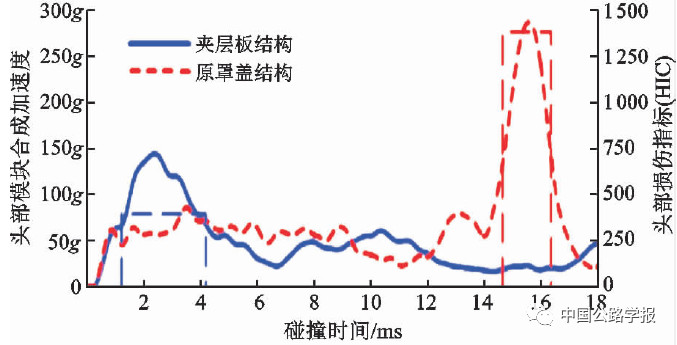
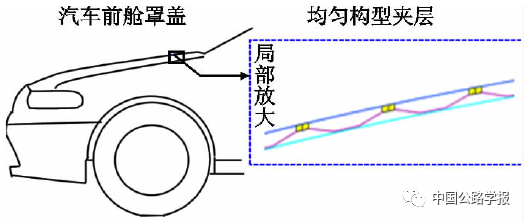
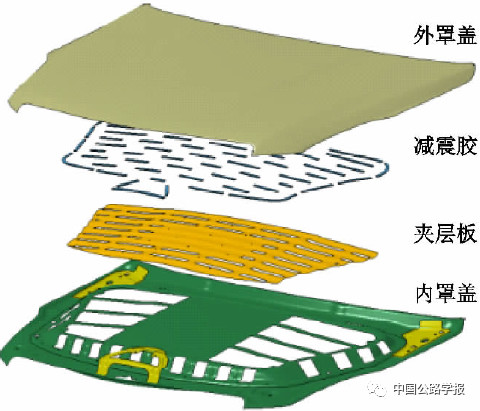
1.2 基于人体模型的行人下肢碰撞损伤研究
在行人与汽车碰撞事故中,行人下肢与保险杠接触形式复杂,膝关节韧带断裂和腿骨骨折等损伤与行人姿态及体型、人车接触速度、接触位置和接触方向以及汽车前端结构设计等高度相关。人体有限元模型是近年新发展起来的用于碰撞损伤研究和碰撞保护设计的工具,可以从人体组织层面评估损伤,基于真实的损伤情况来改进人体碰撞保护设计[7-8]。人体模型本身也需要在研究和应用中改进。针对行人下肢碰撞保护的汽车前端结构设计中同样呈现碰撞工况复杂和吸能空间限定的难点,我们采用先进的人体数值模型作为工具,先解析出复杂工况下行人下肢碰撞响应与损伤机理,找出车身造型与结构变量对损伤的影响规律(图3),进而建立一个基于人体损伤预测的保险杠设计系统[9-10],弥补了基于法规设计的不足[11]。采用接触刚度可变的保险杠结构,可以实现区分行人碰撞和整车碰撞不同工况的碰撞响应控制[12]。
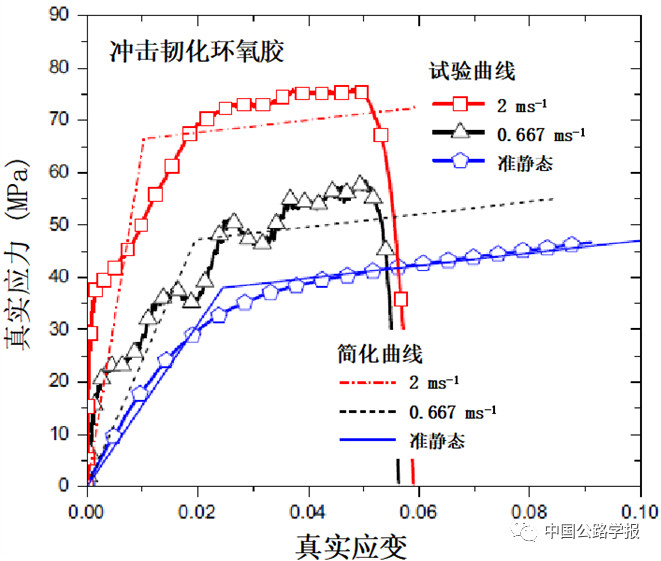
道路事故数据分析表明,行人下肢损伤与姿态和体型显著相关。为了研究其影响机理,我们基于解剖学特征的人体有限元模型,建立姿态调整快速计算框架,在此基础上增加人体几何统计学模型,开发参数化行人人体有限元模型,作为多种体型特征行人碰撞和损伤研究的工作平台。采用以上算法和平台,发现膝关节自然弯曲可降低损伤风险的机理,解释肥胖所增加的惯性力与下肢损伤风险提高的关系,为汽车的自适应行人保护结构提供一定的设计依据[13-14](图 4)。
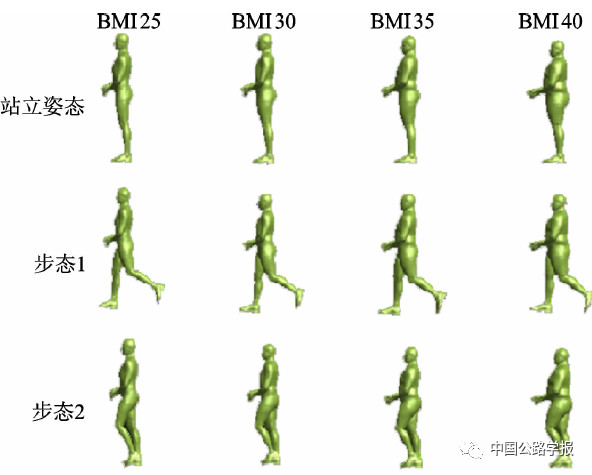
1.3 满足复杂工况的乘员碰撞响应控制技术
汽车碰撞事故中,外载荷的形式与强度、乘员状态以及乘员约束保护决定车内乘员碰撞损伤风险。小型车和轻量化车的碰撞波形比普通轿车更为复杂和严苛,车辆前部结构吸能位移和乘员舱内的生存空间有限,使得在强冲击载荷作用下,通过汽车前端结构碰撞变形和乘员约束系统作用传递到乘员身体上的载荷很难均匀,加上乘员状态多样性,导致人体承受的载荷在时间和空间上呈现很强的非均匀分布特性,能量吸收空间利用率低下。
针对乘员整体碰撞响应姿态控制的难题,一个可能的解决策略是建立基于膝部挡板、座椅姿态和刚度调节的乘员碰撞响应姿态控制方法(图 5),核心是利用碰撞初始的高惯性力来平衡碰撞后期的吸能位移,充分利用外载荷冲击在时间历程和空间分布的特点来控制人体碰撞响应姿态,通过控制乘员躯干和下肢约束力的作用时间及强度来控制乘员的碰撞响应姿态,使其在碰撞历程中经历更为均衡的约束力,优化安全系统的变形模式和响应次序,提高能量吸收效率,实现损伤敏感部位冲击力的降低,从而最小化乘员损伤风险[15-17]。
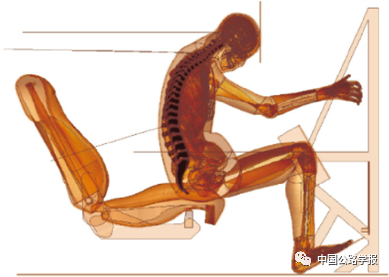
滑动吸能座椅技术(图 6)与后倾乘员的姿态控制和碰撞保护技术,不仅能有效降低尾撞工况下颈部挥鞭伤的风险,还可与气囊及安全带协同作用,有效控制乘员整体运动姿态,避免乘员发生下潜运动,并在主动、被动一体化技术层面利用主动座椅控制和碰撞动能快速调整后倾乘员姿态[18-25]。
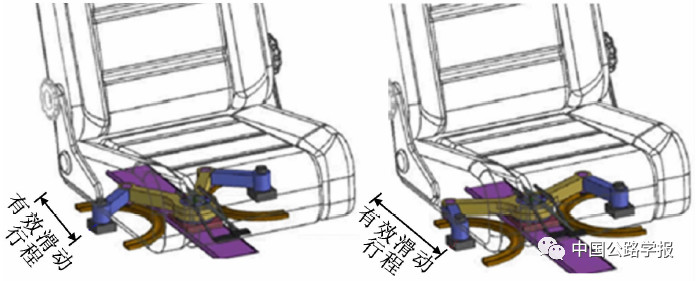
在此基础上,通过对乘员约束构型谱的研究,进一步得到自适应乘员约束系统的关键影响参数和损伤输出之间的关系,实现针对不同乘员身材和碰撞强度时,乘员约束载荷可调(图 7),可进一步使系统成为主动、被动一体化的自适应乘员约束系统,对复杂碰撞工况和中国人体特征提供有针对性的碰撞保护[26]。
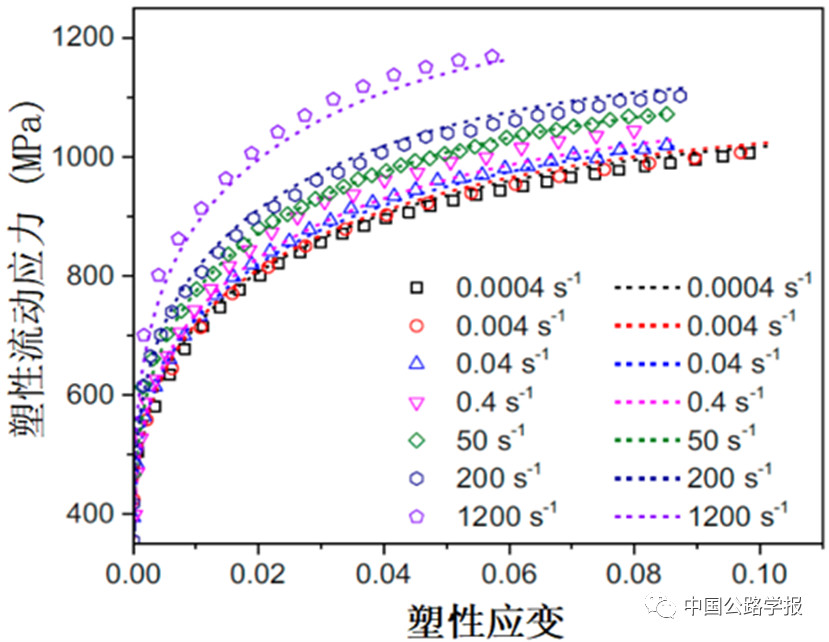
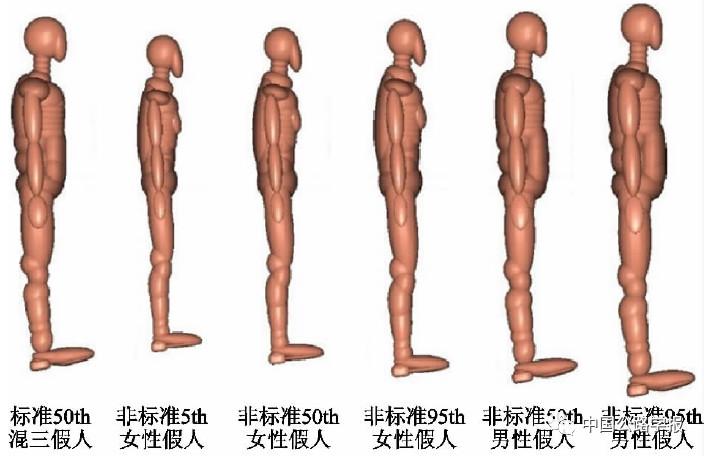
综上,针对实际交通事故的复杂工况和未来智能交通中可能出现的多样乘员姿态和汽车内饰环境,乘员碰撞保护设计思想应包括:通过座椅滑动来吸收碰撞能量;通过主动调节座椅姿态和刚度来控制乘员碰撞响应姿态;通过对乘员身体施加均衡约束载荷来降低整体损伤风险。三者相辅相成,构成了以座椅为核心的乘员约束系统设计理论,为未来智能汽车中具有多种朝向和姿态的乘员碰撞保护奠定了技术基础。
1.4 适应多方向碰撞响应的碰撞假人技术
作为汽车碰撞安全性的人体损伤评价装置,国际上现有的碰撞假人仅能适应单一工况,分为正面碰撞假人、侧面碰撞假人和后面碰撞假人等。因为实际事故工况复杂,也因为座椅安全带对人体的加载本身就是非对称的,实际道路交通事故中人体所经受的载荷多为斜向碰撞。为实现多工况下对人体损伤的准确评估,如图 8所示,我们研发了具有高生物逼真度的多方向碰撞假人柔性胸部结构,以同时满足正面碰撞、侧面碰撞和斜向碰撞的响应要求,通过离散式构型的设计满足安全带对胸部的局部侵入变形响应[27];研发了行人四自由度膝关节下肢模块,以实现在多个碰撞方向上能更好的再现实际人车碰撞中的复杂工况,更真实的表征行人下肢模块与保险杠变形交互作用时的响应[28-29]。
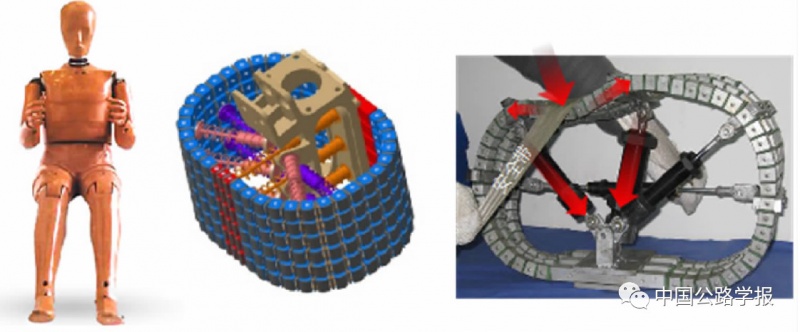
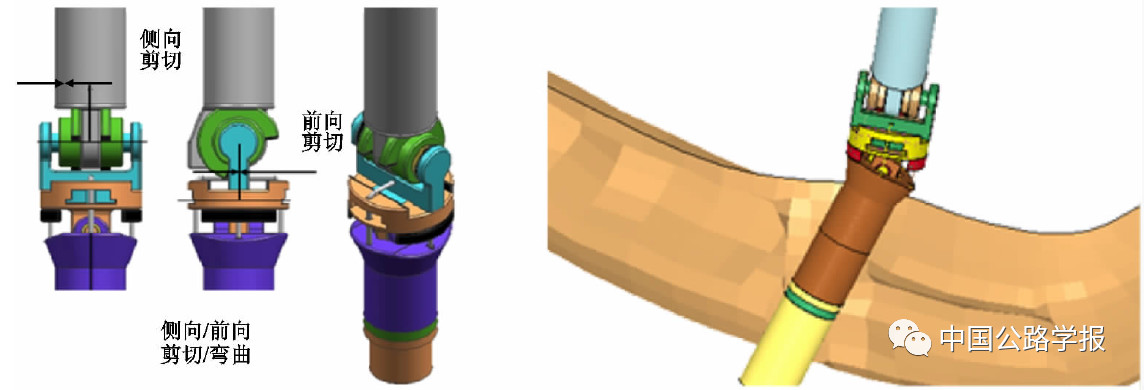
2 轻质车身材料的碰撞大变形表征及失效预测技术
2.1 材料冲击力学测试关键技术
车身结构轻量化需要对材料的性能和材料的应用条件有全面深入的认识。对于汽车结构而言,耐撞性是最需要优先保障的性能之一。在汽车碰撞事故中,车身关键结构的材料经历动态冲击、塑性变形甚至失效的过程。为建立准确高效的仿真预测能力,需要全面掌握材料在动态冲击下的力学特性,认识其变形和破坏机理。
中高应变率材料冲击试验中载荷测量失真一直是材料冲击力学测试中的一个难题,在102s-1应变率量级的材料力学性能测试中,载荷传感器获得的冲击载荷信号耦合了传递路径的系统响应,呈现明显的振荡,难以从中提取正确的材料自身的力学响应,无法满足车身结构耐撞性及轻量化的设计仿真分析需求。
针对冲击测试系统核心组件的载荷传递路径,通过分析中高应变率冲击力学性能测试中载荷信号振荡失真的根源(图 9),本团队发现,载荷信号与测试过程中的载荷输入、试样尺寸、夹持方式和测量装置密切相关,进而揭示了夹具和测量组件的质量、刚度和阻尼对系统振荡的影响规律,提出通过调整载荷测量环节固有频率消除系统振荡的关键思路,针对包含被测对象在内的冲击测试系统整体进行优化,提出了集成载荷传感器的轻型夹具工装设计方法。将该方法用于中高应变率下多种材料动态试验,在多个工况下消除了力测量信号中的振荡现象[30-32]。
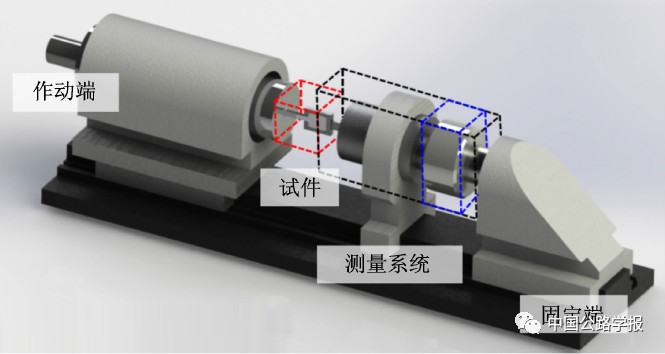
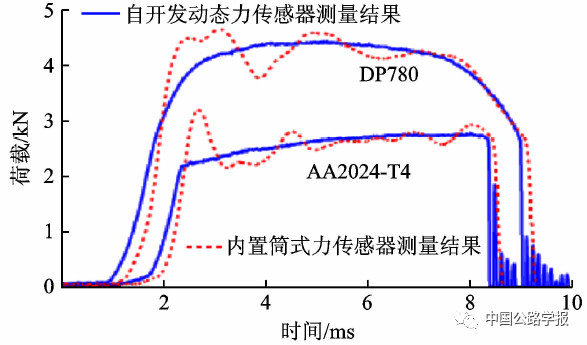
除了测试系统参数外,被测材料的力学属性也影响动态载荷测量信号质量。对于具有明显屈服平台的材料(例如HSLA340),当目标应变率达到200s-1以上,使用前述集成式轻质载荷传感器也难以有效抑制载荷信号振荡,这是因为被测材料的切线模量在弹塑性过渡区有急剧变化,该扰动放大了测试系统谐振的幅度,给该类材料的硬化行为表征带来困难。对此,本团队提出了先低速预加载试件过屈服点后卸载,再进行高速加载的实验方案,人工干预越过初始屈服平台的影响,相关材料的动态试验结果表明,该方法有助于更准确地辨识中高应变率下该类材料的塑性力学行为[33]。
2.2 轻量化材料碰撞失效机理与预测技术
汽车碰撞事故中材料变形和断裂往往是发生在复杂应力状态和中高应变率下,而目前多数材料失效表征都仅针对单向拉伸应力状态,也缺乏复杂应力状态下材料变形和断裂模型,使得仿真计算对车身结构和连接接头断裂的预测不准。本团队基于精细化的材料力学试验,揭示中高应变率范围内轻质合金和高强钢材料力学特性的变化规律,建立考虑应变率和应力状态耦合影响的轻质合金塑性和断裂表征模型[34-37];提出了多级应变率下某类高强钢的统一塑性硬化主曲线理论,由此建立该类材料的应变率相关塑性硬化特性表征模型[38];揭示应变率、温度与应力状态对热塑性高分子材料屈服、流动和断裂特性的影响规律,建立完整的热塑性高分子材料大变形和断裂力学行为表征方法[39-40](图 10);揭示了保险杠泡沫吸能材料加卸载过程中的应力软化效应,建立了相应的仿真分析方法[41-42];针对碳纤维三维编织复合材料,通过试验和仿真,研究了编织和铺层形式对碳纤维复合材料结构耐撞性能的影响[43-44]。
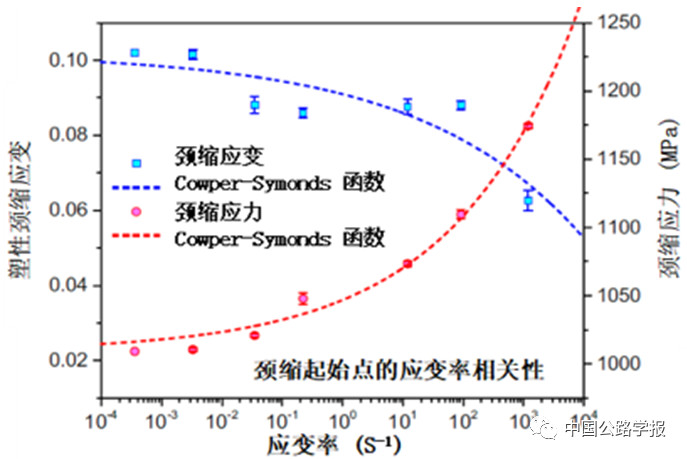
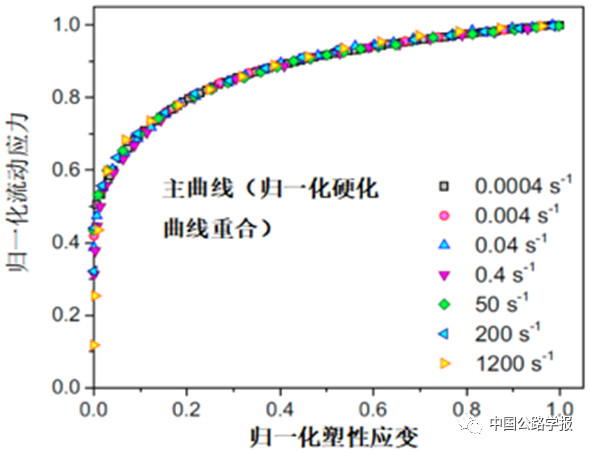
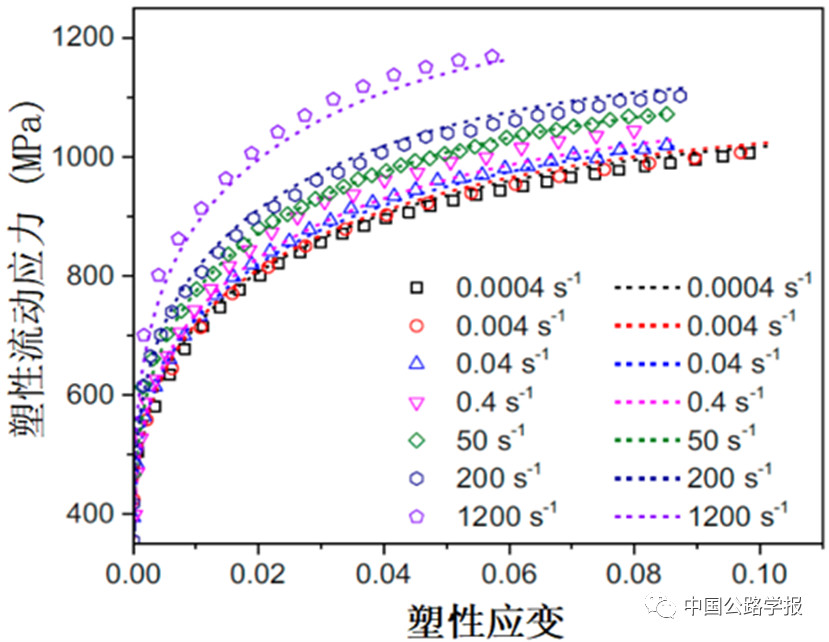
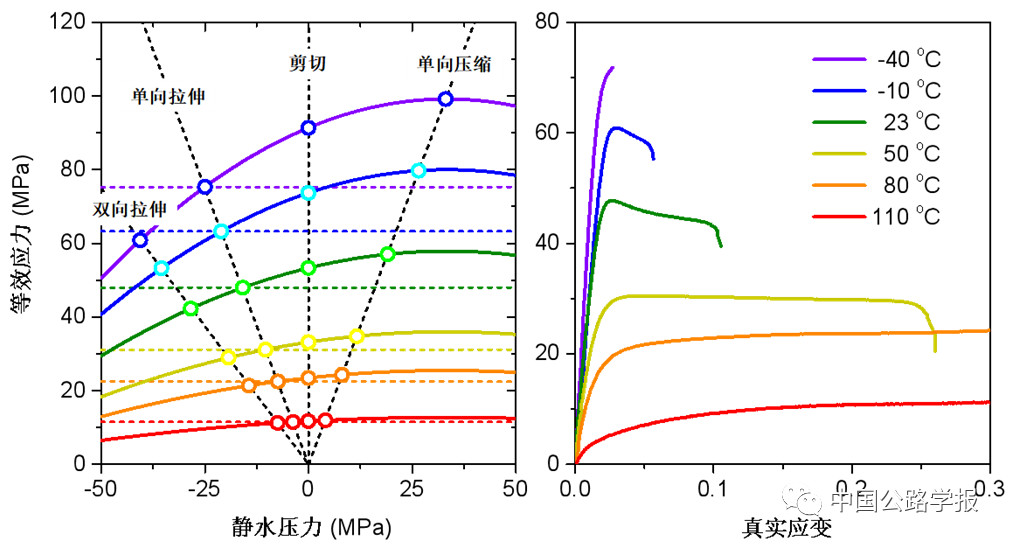
2.3 结构连接接头的碰撞失效预测技术
多材料混用的轻量化车身结构不再采用点焊作为结构连接的唯一方式,而是根据被连接材料的属性选择点焊、胶粘、铆接等方式或混合连接方式,这些连接方式在碰撞载荷下的失效以及与被连接结构和材料的交互作用机理非常复杂,缺乏相应的仿真预测模型。在轻量化车身结构连接接头的研究中(图 11),本团队开发冲击韧化环氧胶粘剂的应变率相关材料模型和失效准则[45],提出点焊接头拉拔失效的等效模拟方法[46],揭示焊点排布对薄壁结构变形模式和吸能特性的影响规律[47]。在系统开展的焊点与胶接混合连接碰撞失效表征和预测技术研究中,本团队揭示点焊和胶接连接在典型载荷作用下的互补机制,建立焊点与胶接混合连接接头的高效仿真模型[48-49];在结构层次上,证明了焊点在胶层裂纹扩展中有效发挥了止裂作用,胶层显著缓解结构性能对焊点数量的依赖程度[48-49],为胶焊连接结构的轻量化设计提供依据。
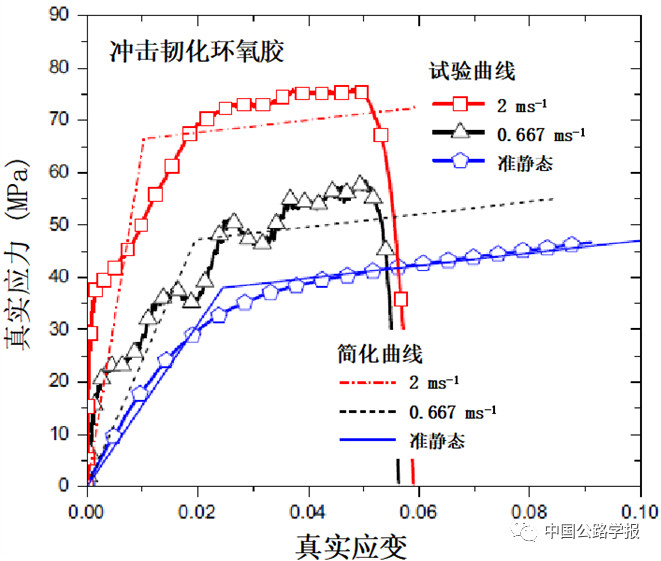
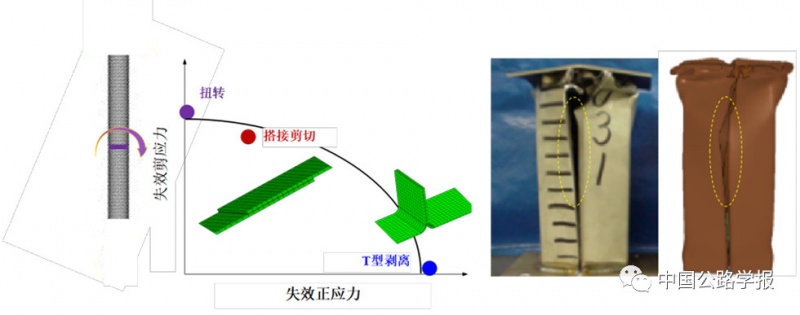
图11 胶接接头和结构碰撞失效表征及预测
基于上述研究开发的材料和接头在复杂应力状态下的变形表征技术、断裂预测模型及相关基础数据库[34-47][50],本团队与企业合作,基于轻量化、工艺和成本等要求,开发材料选择、连接匹配的优化流程,建立冲击载荷下结构中材料和接头失效的诱导和控制策略。
3 车用动力电池的碰撞失效预测与抗撞设计技术
3.1 车用动力电池碰撞挤压工况下的变形失效机理与损伤容限
电芯受到局部挤压导致短路失效是电动汽车碰撞事故中危险性比较高的典型工况,亟待研究其变形失效再载荷形式、强度以及荷电状态等不同作用下的影响因素,也需要找出电芯在不同工况下不发生短路失效所能承受的最大载荷或者最大变形,即所谓的损伤容限。如图12所示,本团队基于试验观测,分析挤压工况下软包电芯、方形硬壳电芯等不同类型电芯的内部损伤积累,发现宏观力学响应特征、断裂模式与局部损伤演化存在高度一致性[51-52]。在这些电芯的球头挤压试验中,均发现挤压力对挤压位移曲线的斜率拐点对应着内部损伤演化的起始时刻。这个发现为建立有效的电池挤压失效判据提供基础,明确承受机械载荷的动力电池在发生内短路之前允许一定变形量。以此为核心可建立电池碰撞保护策略,实现电池包轻量化设计。
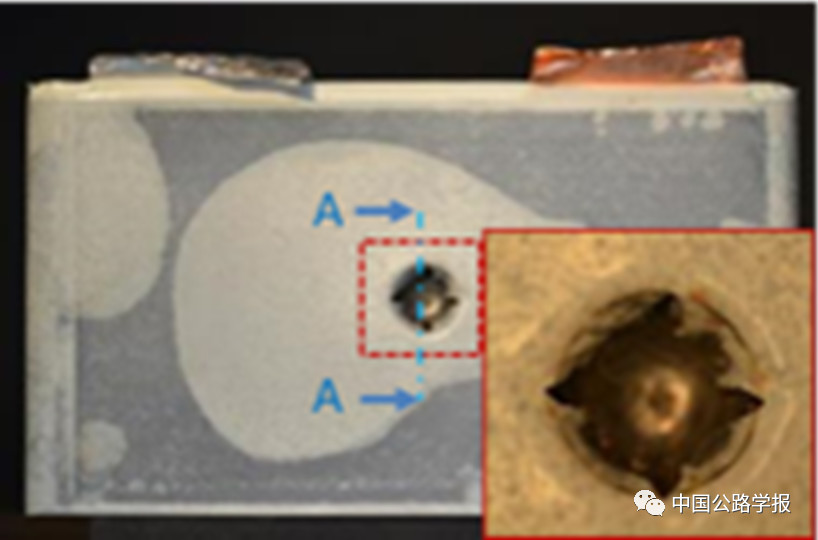
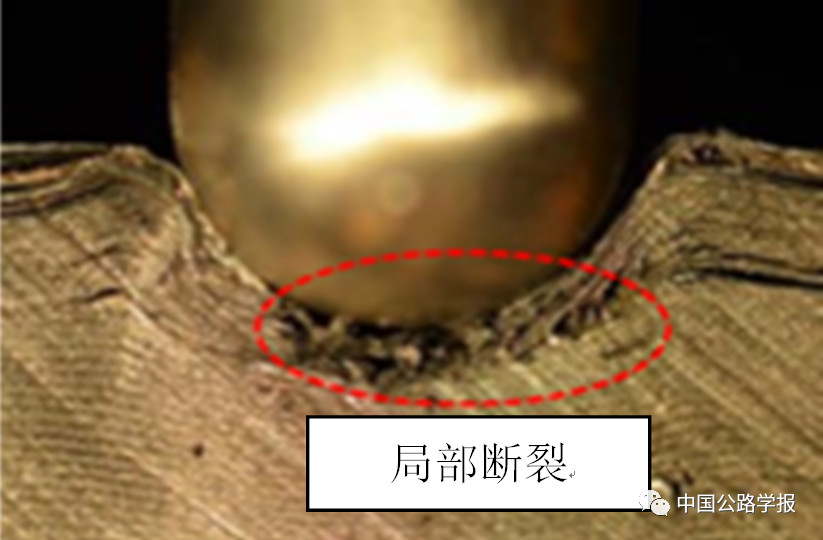
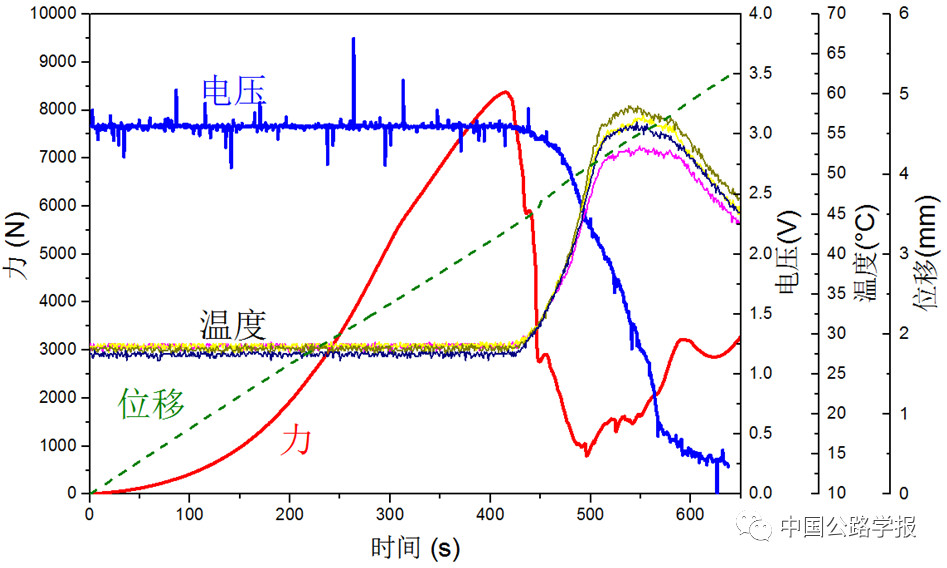
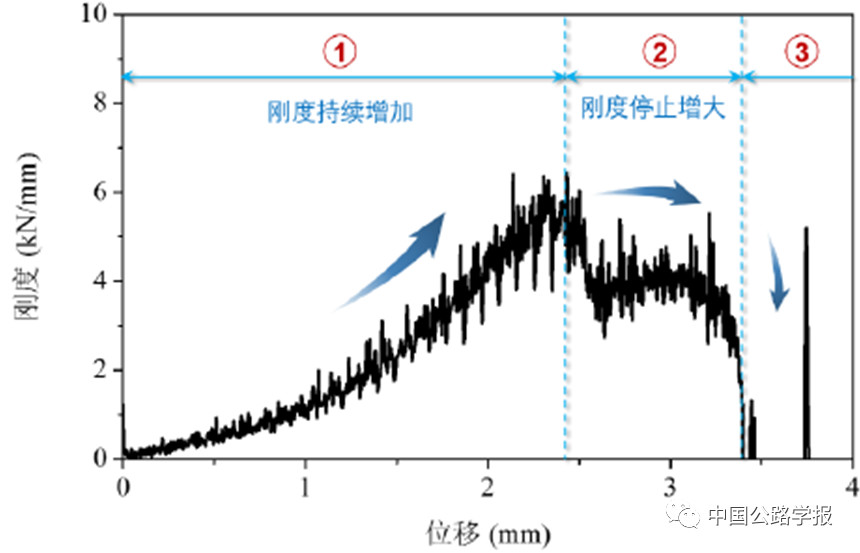
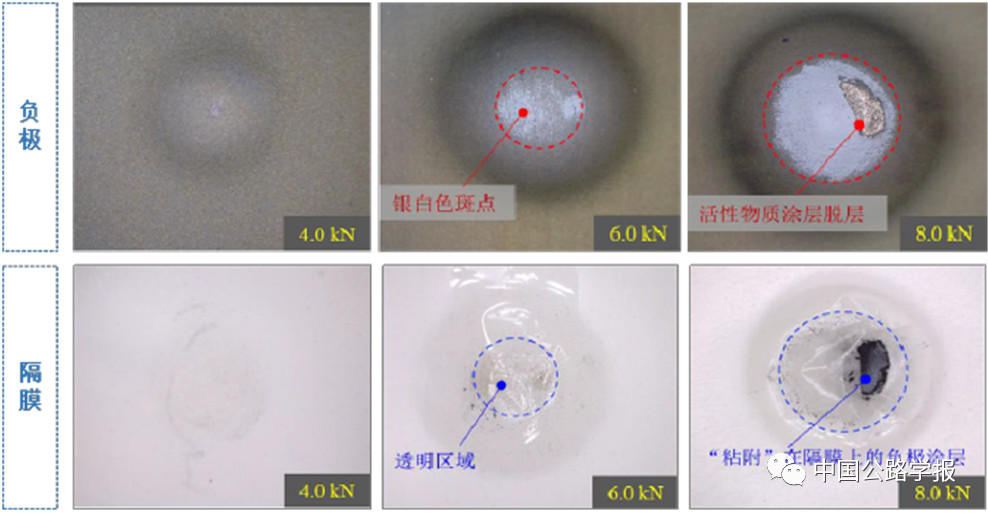
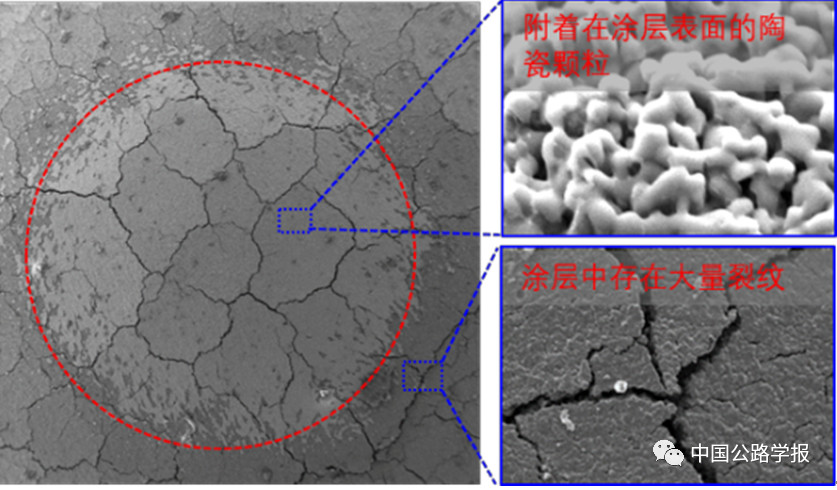
在上述刚度拐点附近取多个载荷水平,通过挤压试验得到对应的多个变形电芯样品,分别进行拆解,并利用光学显微镜和扫描电镜观察电芯内部组分材料形貌,探究电芯挤压变形过程中的内部损伤特征,包括电极活性涂层的颗粒压裂和滑移、电极活性涂层从金属集流体上的脱落、隔膜局部压缩减薄、隔膜陶瓷涂层脱附、电极活性涂层与隔膜的局部粘连等,试验结果表明电芯内部发生的材料和界面不可逆损伤累积是形成最终局部断裂和内短路的主导因素,如图12 (b)所示。
对达到挤压峰值力的电池进行拆解观察,发现内部组分材料断裂位置与损伤累积显著区域相吻合[53-54],很好地佐证了损伤累积引发局部断裂、进而触发内短路的失效机理。在不同形式的挤压试验中,观察到电芯的局部断裂模式和位置存在差异,并且对电热响应影响显著。
在不同加载速率下开展电芯挤压变形与失效机理研究并分析其差异,试验结果表明,动态冲击载荷下电芯的结构刚度增大,内短路时刻对应的变形量减小和载荷降低,即电池在动态载荷下变形的安全阈值更低。上述现象体现电池力学响应特有的率相关性。通过干湿状态电芯的对比试验,结合解析模型与液固耦合数值模型分析,揭示电芯中的电解液在碰撞冲击下具有显著的动态强化效应和破裂诱导作用,这也是动静态挤压加载下电芯力学响应差异的主要原因[55]。
对不同形状电池进行挤压试验发现了两种断裂模式,双轴拉伸引起的面内断裂和剪切导致的层间断裂。层间断裂影响开路电压变化的快慢,层间断裂越显著,电压下降越快。此外,断裂模式还会影响内短路区域和位置,进而影响热和温度[56]。
在电池模组层面,本团队基于落锤试验台(图13)建立了电池模组冲击测试规程,开展多种构型电池模组冲击试验,考察不同冲头、不同冲击速度和方向对电池模组碰撞响应的影响规律[57-58]。

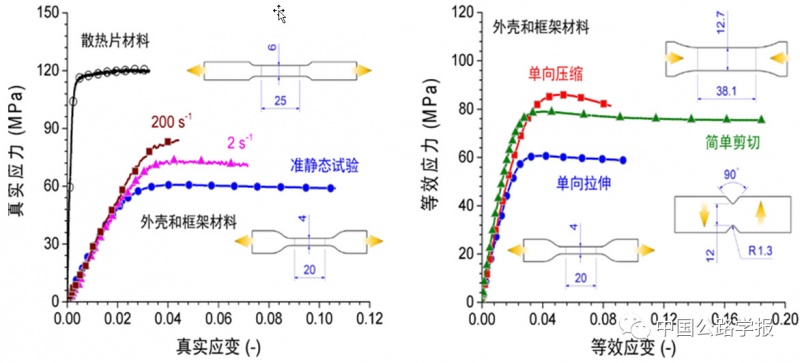

3.2 车用动力电池的碰撞失效预测模型
对于电动汽车碰撞安全性来说,现阶段还缺乏合理的动力电池仿真模型辅助动力电池的安全保护设计,动力电池碰撞变形和失效的准确预测,已成为相关碰撞防护设计的技术盲区。
由于内部多层结构特点,电池的特征尺度跨越了多个量级,如果按最小特征尺度建模,一个完整的电芯模型单元数量在百万量级以上,必然导致高昂的计算成本。因此在建立电芯数值模型时,在保证一定的模拟精度前提下,有必要采用合理等效,选择合适的材料模型和单元类型,减少单元数量,以提高计算效率。
本团队建立基于精细化、半均质化和均质化模型的多级模型开发和参数传递策略[55][58]。对电芯主体层状结构宏观力学特性实施了均质化等效表征,有效模拟电芯结构力学行为的拉压不对称性、各向异性和应变率相关性(图13);量化局部应力应变参数与电芯内短路的关联性,建立基于等效应变、考虑受力状态影响的电芯损伤判据,用于预测多种挤压工况的电芯失效。
3.3 车用动力电池的抗撞设计技术及电动汽车碰撞运动姿态控制策略
面向车用动力电池的碰撞保护和面向乘员的碰撞保护涉及的危险工况不完全相同,由于电池箱多布置在乘员舱的地板上,侧面柱撞、托底和底部异物冲击成为相对比较危险的工况。针对2013年美国的一起电动车底部异物碰撞引发的电池着火事故(图14),本团队对该碰撞工况的边界条件、撞击过程中底部护板的破断模式以及局部电池的挤压变形进行了再现分析[59],对比分析多种底部碰撞保护结构形式,提出了兼顾轻量化和底部碰撞保护性能的波纹构型填充的三明治底部护板结构[60]。
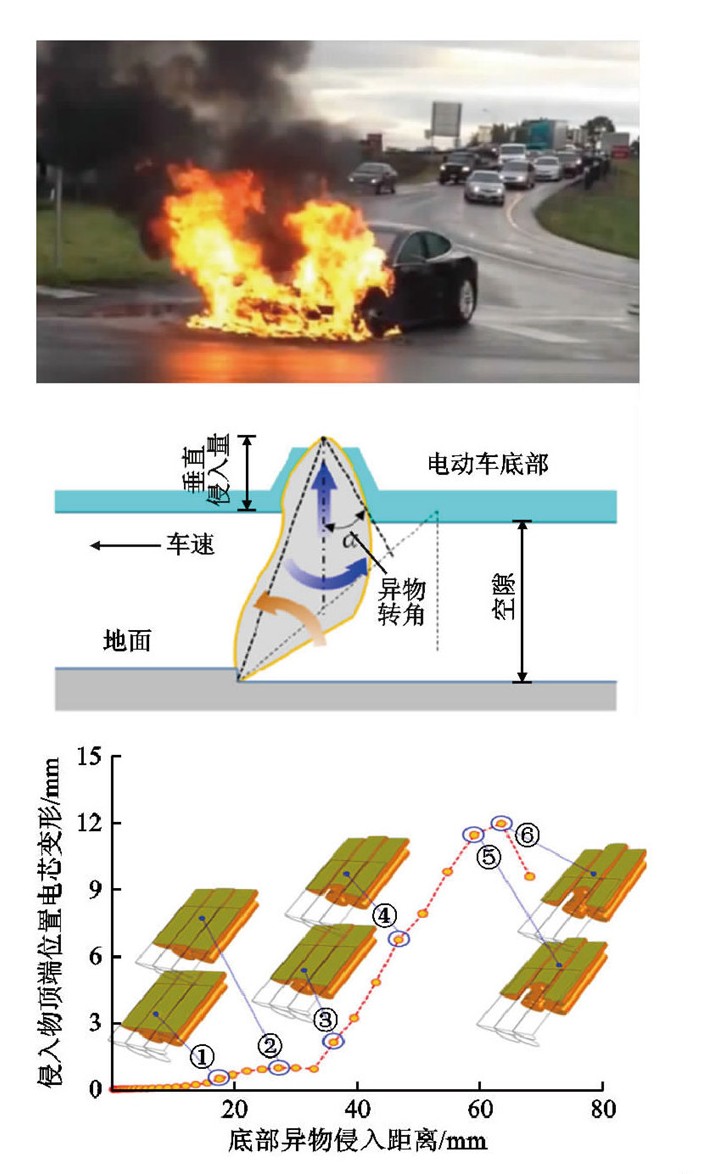
从弥补电池能量密度不足和保证续航里程的角度,小型轻量化电动车有较大的优势。本团队研究发现,小型轻量化电动车的碰撞响应对电池排布方式更为敏感,电池布置很大程度上影响着整车质心位置和转动惯量,进而影响碰撞响应(图15)。针对常见电池布置方式、典型碰撞工况以及不同碰撞强度开展多工况碰撞仿真分析,结果表明,在正面全宽碰撞中,车辆重心越高,碰撞中俯仰运动越大,初始动能转化为重力势能越多;在偏置碰撞中,车辆重心越低,碰撞中俯仰运动越小,后轮与地面的接触压力越大,车辆偏转运动所需的摩擦能耗越大。通过电池包布置方式调节车辆重心,可优化控制电动车在碰撞过程中的俯仰和偏转等运动姿态,从而为碰撞安全性能优化引入新的控制因素[61],基于此形成将单方向碰撞转化为复合运动响应的碰撞运动姿态控制策略,有利于解决小型电动汽车的电池布置空间和碰撞变形吸能位移的设计冲突。
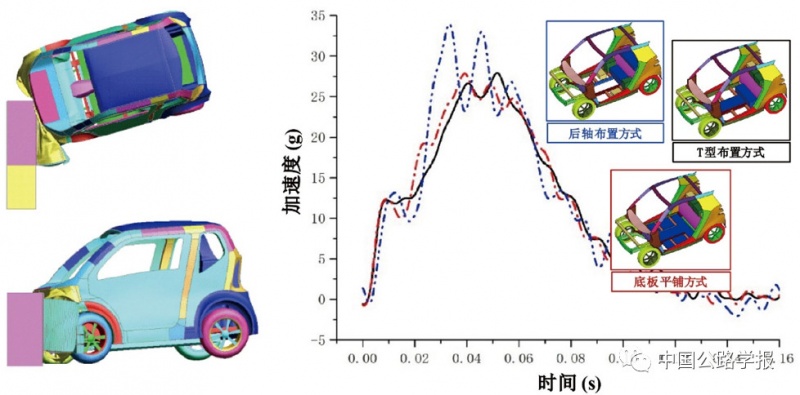
图15 电动汽车碰撞响应分析
4 结语
研究汽车碰撞安全与轻量化的技术挑战性课题,需要以冲击力学为基础,并与碰撞损伤生物力学、材料技术、工艺技术、数字化仿真技术和结构优化设计等学科交叉,其难点主要源于工程实际问题的复杂性、汽车碰撞吸能位移有限、轻量化和安全裕量两方面设计要求的冲突以及制造成本的约束等。
人员碰撞保护方面的主要难题是,真实碰撞事故工况非常复杂,能量吸收空间受限,使整个系统呈现强非线性。本团队研发的夹层式汽车前舱罩盖技术依据冲击动力学理论,通过结构优化提高冲击响应在时间历程上的均匀性,进而提升空间资源的利用效率;针对碰撞工况和乘员状态可调的自适应乘员碰撞保护技术,给未来行车环境中多样性乘坐环境下的智能碰撞保护和损伤控制奠定了技术基础。
轻量化车身结构设计需要应用仿真计算来提高抗碰撞设计效率,技术瓶颈是对复杂应力状态下的材料失效进行准确预测。本团队对各类车身材料的精细化力学表征研究以及所研发的冲击力测量信号振荡抑制技术,提高了材料和接头在复杂应力下的碰撞断裂预报精度;同时,在确保一定精度的情况下通过建立等效简化模型来降低仿真计算量,为断裂预报在整车碰撞安全性设计中的应用提供了实用的计算模型和参数。
电动汽车动力电池在碰撞下的短路失效机理和预测是近年来汽车碰撞安全方面的一个新的难题。由于缺乏电池破坏和热失控的预测模型,使得电池的碰撞保护和电动车的轻量化设计更多依赖经验。本团队在国际上率先给出了动力电池的碰撞损伤容限和短路发生判据,解析了电芯在机械载荷作用下材料破坏诱发短路的机理,研发了高精度电池碰撞响应的数值模型,提出了电池碰撞热失控风险可控下的电池包减重策略,应用于车用动力电池的碰撞安全评估和抗撞设计。
本团队聚焦汽车轻量化与电动化碰撞安全关键技术难题,以真实应用场景和汽车碰撞设计为对象,以人体和材料的损伤控制和失效预测为目标,开展材料和损伤层面的基础性研究,并依托与国内外整车企业的合作,把基础研究成果应用于实际工程设计。本团队的研究和应用实践表明,以应用为导向的基础研究对汽车产品技术提升具有重要意义。
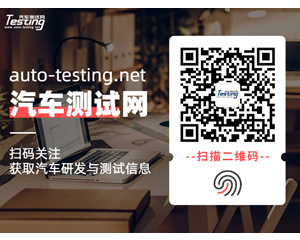
最新资讯
-
浅谈有关示波器的ENOB,是否和你理解的一样
2025-07-30 12:41
-
聚焦AECS国标落地!车载事故紧急呼叫系统开
2025-07-30 12:40
-
罗德与施瓦茨成功验证下一代紧急呼叫系统符
2025-07-30 12:39
-
艾默生扩大集中式测试管理平台覆盖范围,助
2025-07-30 12:01
-
辐射亚太,链接全球——采埃孚再制造战略的
2025-07-30 11:46